Facility Solutions
Products That Add Reliability and Efficiency to Gas Lift Operations
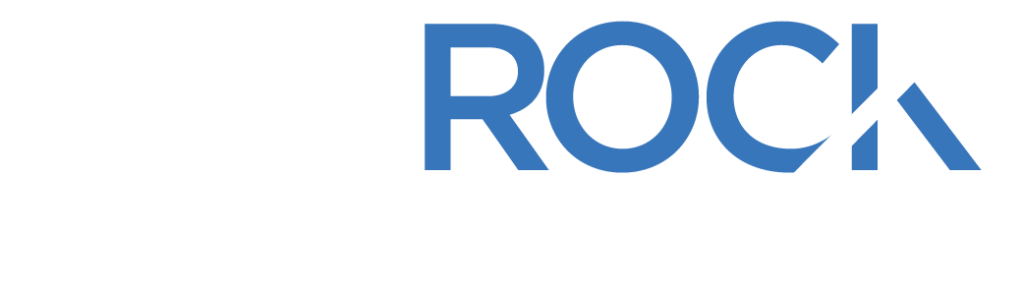
For Liftrock, the goal has always been to improve the efficiency, accuracy, and reliability of customers’ gas lift operations. Today, the company continues that commitment with three gas lift support products – the Liftrock Injection Control Skid (LICS™), custom-fabricated harmonic filters, and fuel gas conditioning skids.
The Liftrock Injection Control Skid (LICS™)
Recognizing the issues associated with liquids in the injection lines, Liftrock developed a solution, the Liftrock LICS 5000 Injection Control Skid (LICS™). Designed to meet AGA-3 standards, LICS is a fully integrated injection control and measurement system contained on a single manufactured skid. LICS is delivered to the wellsite as a turnkey, skid-mounted injection system, requiring only minimal connection to the wellsite’s injection lines. Installation time and costs are dramatically reduced when compared to conventional wellsite construction.
This fully automated system injects gas at a consistent rate, individually to up to four wells . The LICS utilizes a vertical separator ahead of the injection measurement streams, allowing liquids to be removed before injection. With significantly reduced liquids in the injection stream, freeze-ups are virtually eliminated. In addition, by providing “liquid knock-out” ahead of the injection measurement stream, measurement accuracy is enhanced and downtime is dramatically reduced.
A lower level of liquids in the flow lines also equates to less methanol required, more than 75% less. With less methanol used, the number of associated pumps and tanks required for methanol injection is similarly reduced, further cutting installation and operating costs.
In summary, the advanced LICS™ delivers the following benefits:
- Delivered to the wellsite ready to be connected to the flow lines, dramatically reducing in-field installation time and costs
- Virtually eliminates freeze-ups due to the presence of liquids in the flow lines
- Provides reliable “liquid knock-out” ahead of the injection measurement stream, supporting accurate measurement
- Eliminates the pulsations that hamper measurement accuracy
- Reduces the need for methanol injection by 75% or more, along with the associated equipment required to support methanol injection
- Meets all AGA-3 Standards
Custom-Fabricated Harmonic Filters
With the electrification of gas lift compressors in order to reduce CO2 emissions, power grids are dealing with problematic harmonics being added to the grid due to the use of VFDs. The best way to reduce these harmonics is with the use of harmonic filters.
Liftrock’s custom-fabricated harmonic filters are designed to reduce harmonics in the power system in compliance with IEEE-519. These harmonic filter packages are proven to reduce the disruptions to power
Our industry-leading, custom-fabricated harmonic filters are designed to handle every scenario and loading condition, regardless of voltage imbalance or source impedance. This advanced design can correct for low-voltage conditions from marginal systems and adjust the power factor within the electrical system, protecting equipment and saving money. Key feature of these harmonic filters include:
- 83 – 1000+ amps designs
- Meets or exceeds IEEE-519 requirements
- Fully gasketed NEMA 3R heavy duty enclosure
- Steel skid mounted (not pallets like our competitors)
- Integrated isolation contactor for low load conditions, preventing over-voltage faults
- Internal power distribution blocks
- Thermostat-controlled fan cooling system with filter
- Adaptive to varying power loads
- Extends the service life of electrical equipment
- Generator compatible
- Industry leading 3-year warranty
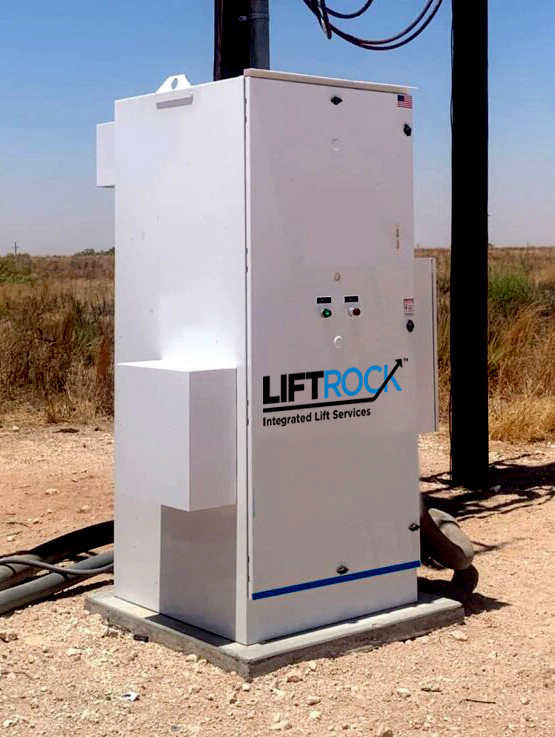
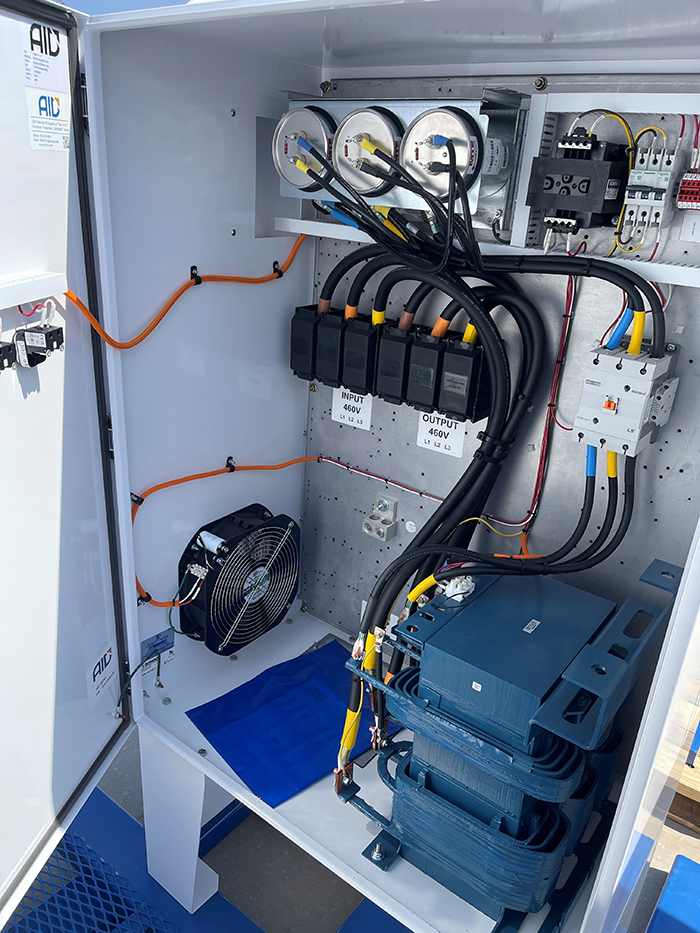
Fuel Gas Conditioning Skids
Designed to increase the horsepower and reliability of engine-driven gas lift compressors, these fuel gas conditioning skids are available in 500, 1500, and 3000 MCFD capacities. Key features of these units include:
- Maximizing NGL recoveries by achieving temperatures as low as -50 degrees Fahrenheit
- Providing lower BTU fuel for wellhead and field operations
- Increasing horsepower and decreasing maintenance due to lowered BTU
- Skid mounting for easy mobilization and installation
- Compact equipment layout on a single skid
- Delivering 1,440 psig MAOP
- Including supply-demand all-pneumatic control system
- Employing high-efficiency heat exchangers
- Allowing easy operation
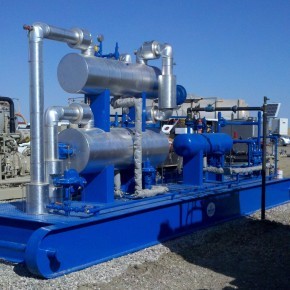